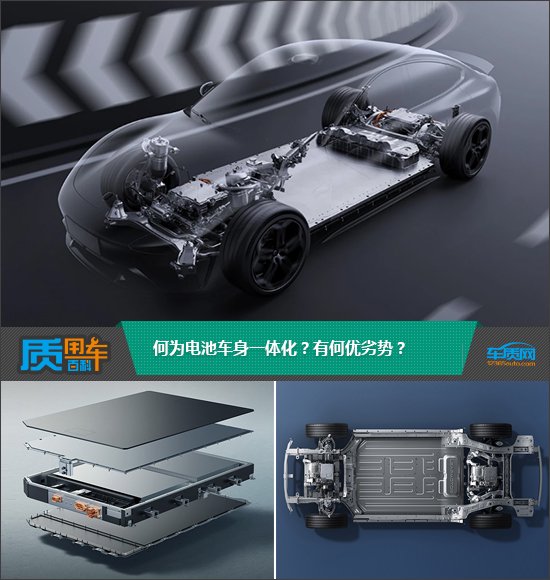
隨着新能源汽車不斷發展,動力電池結構也在持續進化,從早期的獨立電池包模組,逐漸演變爲如今熱門的電池車身一體化設計。電池車身一體化因其高度集成的結構特性受到越來越多汽車企業追捧,在電池材料技術很難實現大舉突破的前提下,讓有限的空間裝載更多的電池,從而實現車輛續航能力和安全性的全面提升。
一、電池車身一體化技術的由來?
早期的電池採用“電芯-電池模組-電池包”的封裝形式,電芯作爲最小單元會首先構成模組,再由模組構成電池包。這樣設計的好處在於將電芯按照獨立的模組加以區分,方便進行管理,並且後期維護也相對簡單。但是,串聯模組之間需要使用大量线纜和結構件,導致電池包重量激增,空間利用率較低,不僅影響車輛續航,還會造成電芯防水、隔熱難處理等安全性問題。
爲了解決上述問題,業界提出了CTP(Cell to Pack)概念,通過取消模組或減少模組,將電芯直接布置在電池包內。典型代表如比亞迪的刀片電池,將電芯直接匯聚成電池包,其空間利用率提高50%。然而,CTP依然只是一種電池包精簡技術,沒有徹底消除线纜和結構件,也無法解決車輛續航和安全問題。
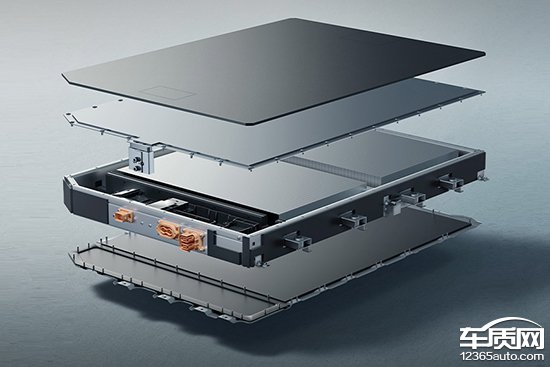
最終,電池車身一體化技術應運而生,通過將電芯直接整合在底盤上,大幅簡化車身线纜和結構件,提高了動力電池能量密度,即單位體積可容納更多的電芯,支持更長的續航裏程。目前,電池車身一體化主要分爲CTC(Cell To Chassis)和CTB(Cell To Body)兩種技術路线。
二、電池車身一體化技術兩種路线有何區別?
CTC和CTB兩種技術路线雖然都屬於電池車身一體化設計,但在結構和具體表現方面又有所不同。
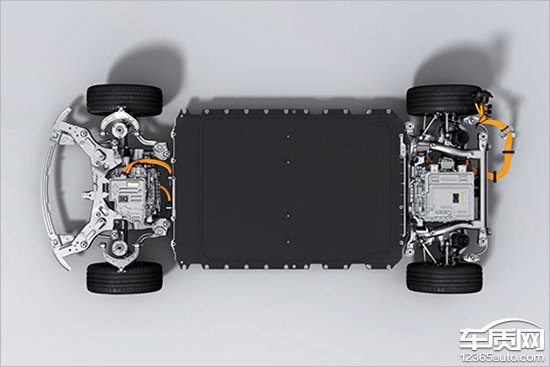
CTC與傳統電池安裝方式的主要區別,在於取消了電池包上蓋板或座艙地板。不同廠家的處理方式略有不同,比如零跑的CTC方案是取消電池包上蓋板,而特斯拉的CTC方案是取消座艙地板。值得一提的是,特斯拉的CTC方案是將車艙橫梁和車內座椅全部集成在電池包上,集成度相比零跑更高。
CTB與CTC類似,都是將電芯直接安裝在底盤上。不過,CTC還是將電池包當作一個單獨需要保護的物體,而比亞迪的CTB是利用刀片電池高安全性和高結構強度的特點,融合進車身的整體設計中來。刀片電池的電芯與整個電池包組成類似蜂窩鋁的結構,本身就可以起到車身結構件的作用。因此,在結構安全和可維修性方面,CTB更勝一籌,對用戶更有利。
標題:質用車:何爲電池車身一體化?有何優劣勢?
地址:https://www.utechfun.com/post/328945.html