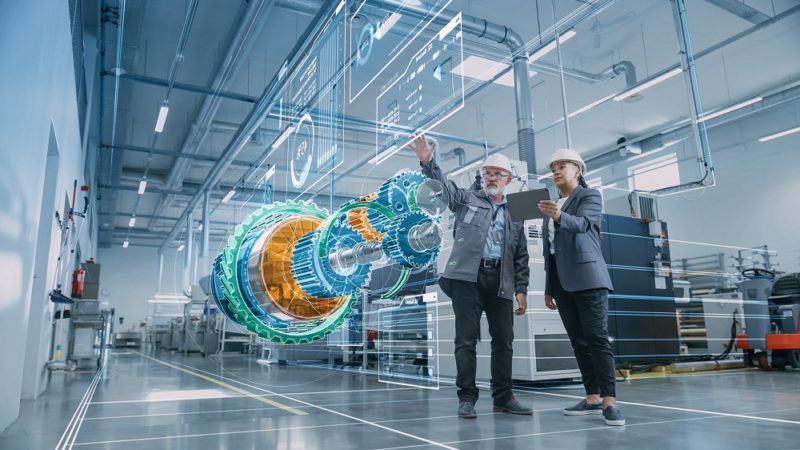
因應地緣政治、全球化生產短鍊化、遠端協作日益盛行等全球變局,台達推出輔以 AI 技術與模型的數位雙生(Digital Twin)解決方案,以協助電子組裝業完美解決少量多樣、產品生命週期縮短、缺工以及高品質生產等挑戰。
在董事長暨執行長鄭平的帶領下,台達自 2015 年推動 DSM 台達智慧製造(Delta Smart Manufacturing)計畫,從設備自動化全面走向智慧化。有了這樣的數位轉型與智慧工廠轉型基礎,台達開發出滿足電子組裝與半導體產業「分散製造、集中管理」需求的解決方案。
台達智能製造軟體新事業發展部處長陳鴻輝表示,為了將原有產能、良率,甚至管理文化完善地複製到全球不同的生產製造場域,台達推出專為分散式製造量身打造的 Line Manager,讓客戶可藉由該軟體連結 IT 與 OT 層,將生產全面數位化並儲存為數據庫,成為在地化生產系統的大腦,管理人員可以遠端集中調控在地產線。
透過台達 DIATwin 數位雙生解決方案,便能在雲端上打造一個擁有現場實體設備及產線所有資訊的虛擬分身設備,客戶可以預先在雲端虛擬產線上進行調試,之後再將全域配方或製程參數下載到當地產線機台上直接生產。不僅如此,DIATwin 還可搭配 AI,打造不斷調適優化為更精準數據模型的封閉迴圈生態系統。
台達智能製造系統整合新事業發展部處長陳霈宇指出,台達 DIATwin 除了能協助企業客戶兼顧品質、成本、交期及服務(Quality, Cost, Delivery, Services,QCDS)以及快速彈性的新產品導入(New Product Introduction,NPI)之外,尤其注重單一機台設備分身的模擬能力,因而能為客戶提供快速的可製造性設計(Design for manufacturing)模擬與完整的企業行動管理(Enterprise Mobile Management)評估。
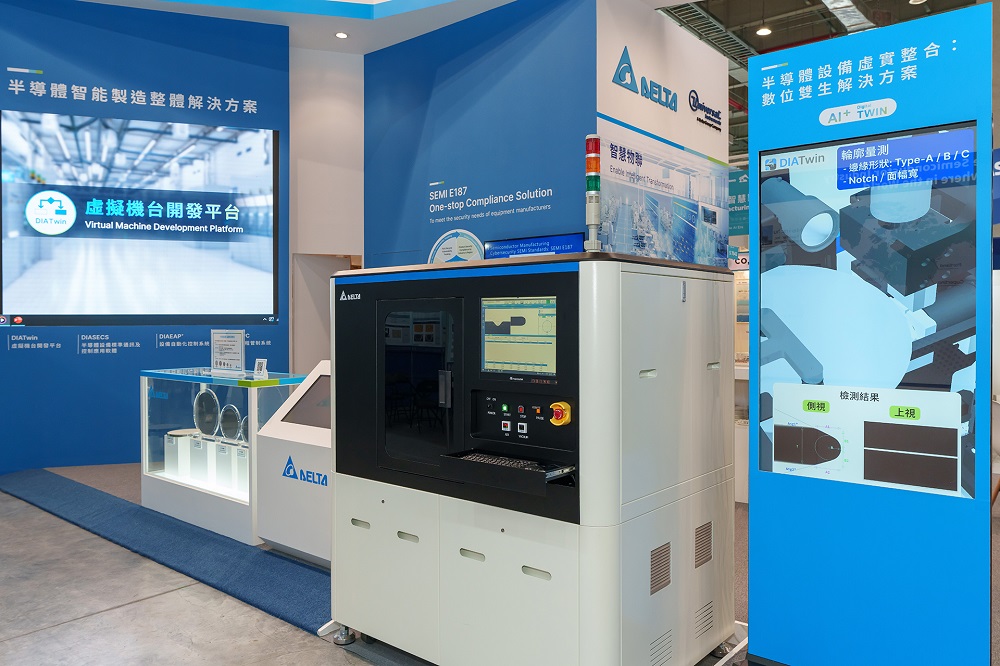
▲ 2024 年國際半導體展 SEMICON Taiwan 上,台達展示 DIATwin 虛擬機台開發平台,示範如何將數位雙生技術應用在前端製程的晶圓輪廓儀。
數位雙生成為縮短開發週期,滿足分散製造需求的最佳解方
數位雙生技術能夠同步消弭虛實差異、降低研發製造風險並縮短產品開發週期,已然成為半導體及電子組裝產業因應在地化製造風潮的最佳解決方案之一。
在地緣政治的衝擊下,當前製造業面臨製程需求複雜多變、產能評估困難、交期難以掌握、開發/測試成本高、參數調機耗時,以及人員經驗難以複製等痛點,透過數位雙生技術的導入,便能為企業帶來顯著的效益與轉機,不僅能加速產線與設備的佈局規劃、提供高擬真的製程模擬,進而降低試誤成本,還能發揮知識傳承與人才培訓的效益。
陳鴻輝強調指出,企業想要導入數位雙生,先決條件就是要有數位化轉型作為升級的基礎。更關鍵的是,必須兼顧精準的資料採集與高擬真度的模擬,如此數位雙生平台才能為實體機台設備提供最佳化的控制代碼、產線配方與製程參數。
陳霈宇補充指出,對於分散式生產,必須同時具備整合設備設計製造、自動控制、軟體開發以及AI應用等四大面向的能力,才能確保數位雙生可以快速有效地在場域落地導入並產生效益。當前許多製造業客戶在導入數位雙生時常見的最大缺口莫過於機台虛擬分身,而建置機台分身正是台達的強項所在。
台達推出的數位雙生解決方案,同時結合 DIATwin 虛擬機台開發平台以及 RTM 虛實整合設備(Reconfigurable Transformer Machine),適用於電子組裝、半導體、車用電子、建築、製鞋以及五金加工取放等產業。
透過高擬真的 3D 製程模擬及參數最佳化模組,DIATwin 能夠極具成本與時間效益地預先進行單機/整線模擬,並在虛擬機台中透過 HiL 虛擬調機(Hardware in Loop)功能持續調試出最佳化的製程參數,大幅提升總公司與在地產線之間以及使用者與設備製造商之間的溝通效益,加速新產品導入與上市時間。
DIATwin 平台能夠高擬真模擬舉凡幹涉、流體力學、動力學等物理現象,並可整合 PLC/PC-based 控制器、工業機器人、伺服器驅動器、感測器、視覺相機與取放夾爪等台達系列產品。換言之,透過高擬真物理引擎以及元件/整機佈局資料庫,能夠彈性滿足不同生產需求,有效提升機台與產線的生產效率。
至於高度模組化的 RTM,能整合各組件的控制核心,賦予機台自動校正機差的能力。除了自動校正與標準模組等功能外,RTM 與 DIATwin 的搭配,更能發揮虛實整合的最大效益,更是因應當前少量多樣生產需求的最佳解決方案。
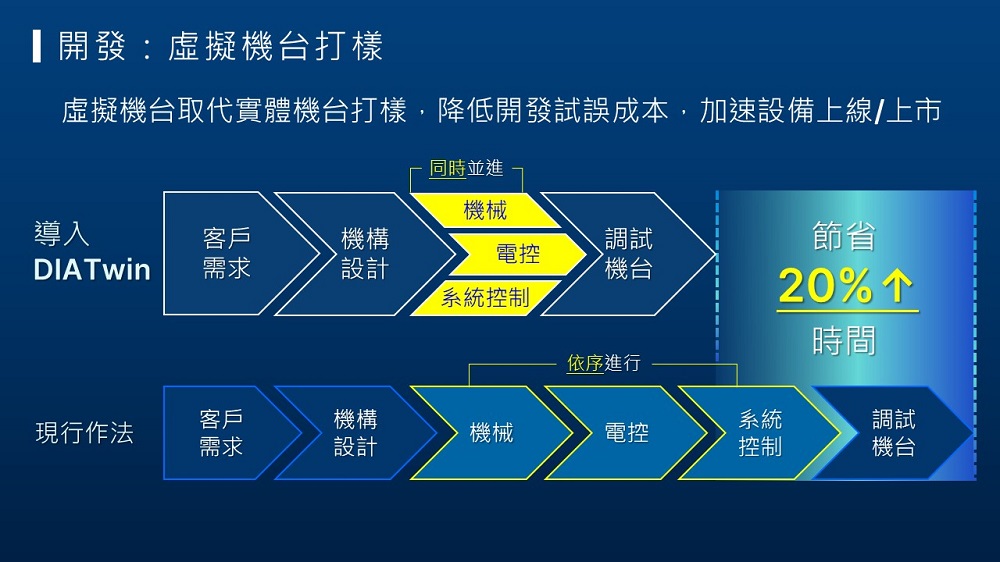
▲ DIATwin 虛擬機台開發平台,透過同步進行的機械、電控與系統控制模擬,成功節省 20% 設備上市時間。
打破 OT 與 IT 溝通障礙,台達 DIACFX 打造智慧工廠機聯網
想要成功導入數位雙生技術,除了前述的數位化基礎、良好數據採集與高擬真模擬之外,為了讓 OT 與 IT 溝通無礙,製造業還必須確保自家設備支援 CFX(Connected Factory Exchange)通訊標準。該標準是 IPC 協會專為電子組裝產業打造的國際通訊標準,係工廠產線設備之間建立 M2M 通訊與機聯網的通訊協定,也是數位雙生的運行基礎。
對此,台達推出電子組裝設備專屬的通訊協定和通用數據模型解決方案 DIACFX,協助客戶快速將該標準導入設備,徹底打破客製化數據通訊成本高昂、OT 與 IT 溝通不良以及上位系統資訊整合不佳等障礙。
該方案並且針對 PC 設備與 PLC 設備等不同程式開發人員分別提供 DIACFX SDK 軟體開發套件以及 DIACFX Box 通訊盒。前者不需開發程式,只需將設備資料傳入 DIACFX SDK 中,該套件會自動處理好一切,包括通訊時的資料模型格式。後者支援多家 PLC 控制器,開發人員只需使用原本熟悉的 PLC 開發,再將資料寫到 PLC 點位,透過簡易設定,DIACFX Box 便可隨插即用,讓產線設備連網。
陳鴻輝表示,傳統工業物聯網多半採用 Rule-based 機制進行各種數據聯網應用,但數位雙生則採用更直覺、敏捷的 Model-based 互聯機制,透過 CFX 標準,即時傳送描述各種設備或產品狀況,例如稼動率及生產履歷等個別資料模型。
AI 加值助力數位雙生,實現更高擬真度的虛擬模擬
數位雙生最引人矚目的特點莫過於在虛擬世界裡打造出和實體設備幾乎一模一樣的高擬真虛擬分身。但以目前的技術而言,即使再高的擬真度仍然會有落差。針對這個問題,陳鴻輝表示,此時AI即派上用場來彌補這個落差。
台達旗下子公司達慧互聯便為客戶提供端到端的專家顧問服務,由機械與製程領域的專家顧問,採集整理客戶專屬的 OT 資料,設計出各種可立即落地的 AI 模型,包括提供預測性維護的 PdM AI、透過視覺辨識技術確保品質的 Quality AI、掌握設備節能減碳狀況與效益的 Green AI,以及降低工安風險的 Safety AI 等模型。透過這些模型,不但可以彌補數位分身的落差,還可加快客戶導入數位分身的腳步。
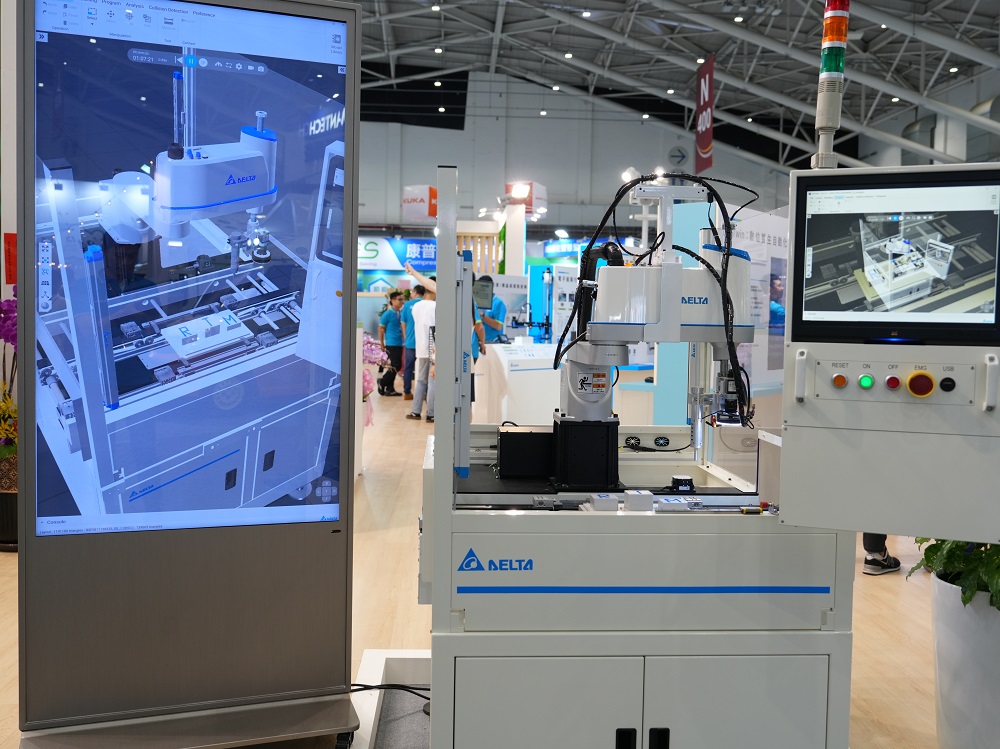
▲ 台達 DIATwin 解決方案,整合 AI 運算與數位虛擬技術,加速機台開發上市。
陳霈宇表示,對於許多製造業廠商而言,數位雙生的導入就像數位轉型一樣需要長時間的投入。台達提供相對精煉的解決方案,再搭配上述 AI 模型顧問服務的導入,相信能協助 90% 以上的客戶加快導入的進程。
台達有許多 DIATwin 搭配 AI 助力廠商提升生產效率的案例,該公司曾助力電子組裝大廠建立高擬真數位噴膠機台,以及包括膠體顏色、噴塗形狀/高度/壓力、I/O 訊號延遲及塗膠分布等精準的資料驅動模型,成功縮減 80% 以上的調機時間。此外,台達曾協助廠商建立涵蓋加速度、夾持力、訊號延遲及真空壓力等精準的資料驅動模型,成功透過 AI 升級取放夾持製程。
落實零人力、零停機、零缺陷,將精力放在創造而非製造上
台達 DIATwin 數位雙生解決方案能分別在售前、開發與調機等不同階段帶給客戶顯著的效益。整體而言,該方案能節省 20% 的設備開發時間,包括新產品設計、建置到調試的時程。台達希望未來能進一步達到 50% 以上。
在售前階段,可透過 Web 3D 互動介面快速建立機種/方案比較、布局評估與幹涉檢測,有助於達成機台設計共識與下單決策。在開發階段,可進行虛擬機台打樣,透過高精度的模擬,展現各種虛實整合應用的效益,不僅有助於提升產線稼動率與產能,更是 OEM 或合約製造商在設備打造之前,便能提前向品牌客戶展示虛擬設備樣貌的提案利器,對於加速設備上線/上市極具助益。
在調機階段,設備上線後也能在虛擬機器上透過示波器驗證進行離線調參,不僅有效縮短調試時間,打造客製專屬的虛擬機台,並且在虛實整合下無縫地將最佳化參數套用在實體機台上,實現機台加值與設備產能優化。
陳霈宇表示,台達推出數位雙生解決方案的宗旨,在於提供產業客戶符合開放標準、最低成本、最佳模擬效果,避免被特定設備、協定或廠商綁定的最佳分散式製造解決方案。
展望未來,陳鴻輝表示,憑藉數位雙生建立的虛實整合系統與在智慧製造累積多年的豐富經驗,台達期望未來能打造自主化智慧工廠,實現零人力、零停機、零缺陷「三零」製造願景,讓「將人的精力與腦力放在創造上而非製造上」的願景獲得完美落實。
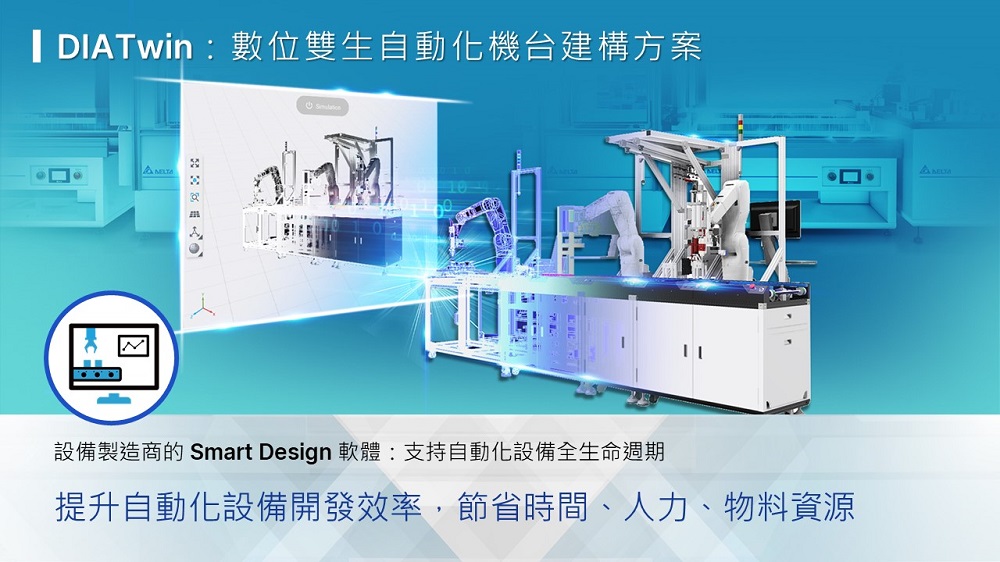
(圖片來源:台達電子)
文章看完覺得有幫助,何不給我們一個鼓勵
想請我們喝幾杯咖啡?

每杯咖啡 65 元
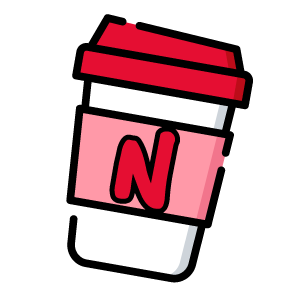
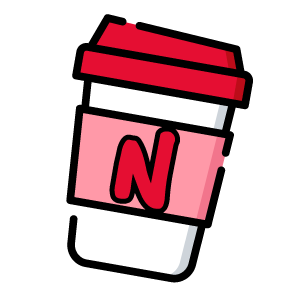
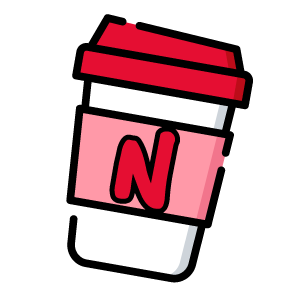
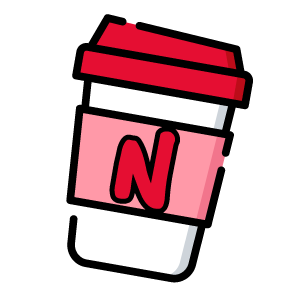
您的咖啡贊助將是讓我們持續走下去的動力

標題:AI 與數位雙生的完美組合!台達為產業推出分散式製造最佳方案
地址:https://www.utechfun.com/post/439600.html