小米汽車偷工減料?看專家如何回應質疑
隨着小米汽車從官宣到產品正式發布、上市,讓車市感受到了何爲破天的流量,也使得汽車线束這一常被忽視的關鍵部件受到了廣泛的關注。
近日以來,關於小米汽車充電线束將傳統的銅材料改爲了鋁材料,引起了人們的廣泛關注和熱議。雖然小米汽車官方表示這一做法是行業的正常發展趨勢,但部分網友仍對此有所質疑,認爲這是“偷工減料”的行爲。
爲深入了解當前行業的最新發展態勢,蓋世汽車特地邀請了萊尼中國的高級產品經理陸曉廣先生以及滬光產品开發中心的總監吳劍先生,共同探討汽車電氣化、智能化演進過程中,汽車线束究竟該如何發展。
減重,仍需被放大來看
汽車线束,通常被認爲是一輛車的中樞神經系統,其將車載電腦與車輛上的各項相關功能連接在了一起。
現階段,傳統燃油車线束均採用銅合金導线,线徑的使用由0.35~25mm,每輛汽車的導线使用如果首尾相連約2KM。以一輛B級轎車的重量來估算,導线的重量約25~30KG,汽車每行駛100KM,車輛將消耗近0.1kg的汽油。
如此重量,約佔汽車總重量1%~2%,其中75%~80%爲導线,端子及接插件佔15%,剩下10%爲外包材料等。
而值得注意的是,伴隨汽車“油轉電”,高壓部件大幅增加,高載流量勢必需要橫截面更粗的銅线來實現。在此背景下,如果是一台1.6-2噸重的B級純電動車,“即便智能化不高,它的整車线束使用量都將達到4km,重量約在60-80kg,佔整車重量約在3%-5%。”蓋世汽車研究院高級總監 王顯斌指出,這一數量還將伴隨電子設備數量的多寡上下浮動。
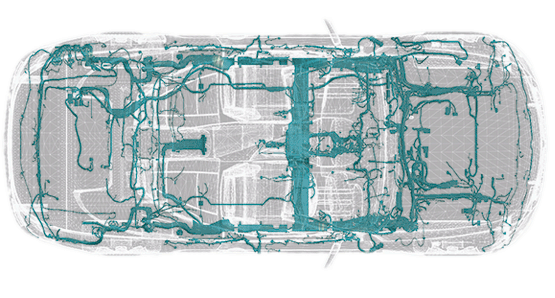
簡而言之,在汽車電氣化、智能化甚至是高壓化演進過程中,汽車线束的導线正變得越來越長,且橫截面更粗,重量勢必水漲船高。
正因如此,在動力電池技術尚未得到顛覆性變革,以及汽車E/E架構尚處在域控制器滲透率較低的背景下,通過更輕量化導线材質來實現线束自身重量的優化,正成爲汽車產業變革過程中的重要措施之一。
銅改鋁,SU7真的不是第一例
“雖然大家對‘銅改鋁’討論非常熱,但從汽車线纜行業發展來講,這項技術早已成熟。”陸曉廣透露道,作爲一家專注於汽車线纜的百年企業,一直以來秉持着TPM战略思路,即技術-產品-市場。當下市場紛紛擾擾,歸根結底性價比仍是第一要義。
不可否認,銅芯導线是目前可知的導電率、安全性表現上較爲出色的導體,但自2005年以來,銅價飆升,鋁作爲最有可能取代銅的導體再次被擺上了台面。
單就現階段來看,“銅的市場售價爲每噸7.5萬元,而鋁僅需每噸2萬元,銅的原材料價格就較鋁貴了3.7倍。”陸曉廣介紹道,“僅看導體,如果用鋁代替銅,將大概節省6~7倍成本。”
成本優勢突顯,其他表現又如何呢?
“相同體積下,銅較鋁約重3.3倍,導電性能是鋁的1.7倍。如果是相同質量下,鋁的體積是銅的3.3倍,導電性能是銅的2倍。”陸曉廣分析認爲,“基於電阻相同或是載流能力相同,銅的質量是鋁的2倍。”
此外,從安裝成本角度考慮,由於鋁導线相對較輕,其在安裝過程中,不需要橋架及穿管,可以節約大量的安裝材料,相比銅導线節省20%-50%的安裝成本。
正因如此,承載電流大、线徑粗,端子和導线拉拔力強的電源线,成爲鋁導线代替銅導线的主要方案被越來越多企業所接受。換言之,便是小米SU7(配置|詢價)並不是業內第一例,而是經過了包括特斯拉、比亞迪等一衆新能源車企驗證過的較爲成熟的方案。
而針對由於抗拉強度較低而帶來的端子壓接拉脫力弱及其他隱性問題,吳劍堅持,在鋁线設計、制造工藝及試驗規範等方面,滬光擁有多年的研究和積累,在小平方鋁线、大平方鋁线、鋁排以及鋁導线適用的端子銅鋁鏈接等多方面均有研究,並已完成多項專利申請。
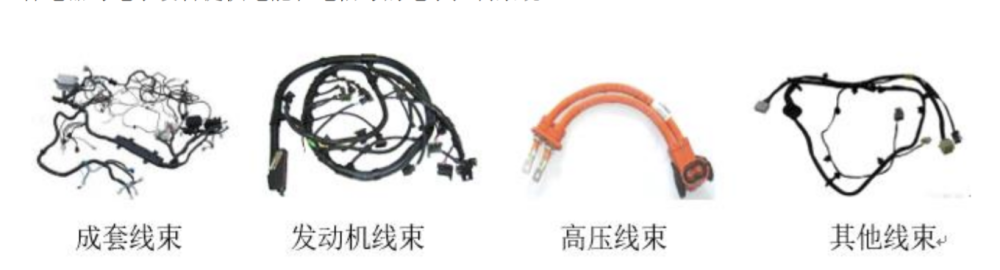
他進一步表示,“材料的切換,並非簡單地基於成本考慮,而是涉及多方面的因素,包括性能、安全、成本及技術發展趨勢。也不是大家理解的簡單替代,是經過了一系列嚴格的產品設計、零件試驗以及車輛路試驗證,其中包括了強化耐久等相關試驗,以確保車輛的性能和安全不受影響。”
回歸小米SU7,其目前話題重點在充電槍等局部應用上,而非100%全車應用,“這也是車企在權衡成本、重量與性能等多層面後的一個綜合選擇。”王顯斌如是說。
智能電動車時代,线束還待變化
如果說,去年是汽車NOA落地元年,那么今年便是各大智能汽車城市NOA規模化落地的關鍵期。體現到整車上,便是感知層、決策層及執行層等相關部件的堆積。
根據泰科電子官網,爲了實現更智能的座艙交互、更高水平的自動駕駛、更低延遲的智能網聯,汽車高速連接器的傳輸速率要求有望從150Mbps(車輛狀況報告、普通IVI系統等功能)逐漸提升至24Gbps(L3~L4級別ADAS、先進IVI系統等功能)。隨着智能化程度的提高,FAKRA、Mini-FAKRA、HSD、車載以太網連接器等高速連接器的應用場景將更加豐富,不同高速連接器將按照傳輸速率與頻率的不同在車內各個領域得以應用。
“高速通訊相關线束對產品的精度、一致性要求已不是傳統的线束制造可以滿足的了。”吳劍分析指出,從選材上來看,將優選高質量、高性能的材料和連接器,以確保信號傳輸的穩定性和可靠性。同時通過優化线束的布局,縮短感知系統和模塊中間的那些距離,還要做一些必要的屏蔽設計,減少電磁幹擾。此外,需進一步提升制造環節的可靠性、穩定性以及可追溯性。
感知層的通訊只是其一。作爲智能駕駛時代執行層的關鍵——底盤,正通過线控改造實現“人機解耦”:將駕駛員的操作命令通過電子控制器傳輸給執行機構,替代方向盤、踏板等傳統機械連接,因而具備了高精度、高安全性、高響應速度等優勢。
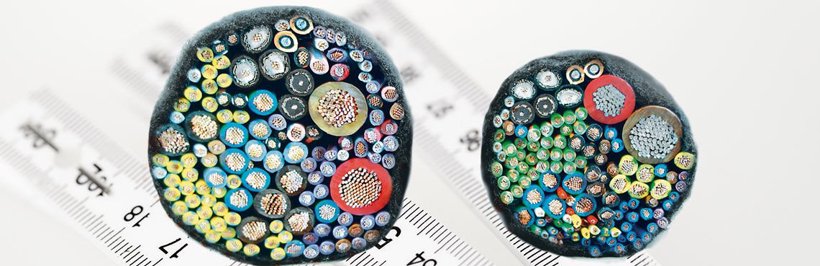
陸曉廣介紹道,以轉向爲例,傳統機械轉向僅需要一個2芯的低頻线束來傳輸輪速信號,但進入线控時代,結構將變得更加復雜,需要4芯甚至多芯,且考慮通訊的穩定性及抗幹擾性,需轉爲數據线纜,來保證信號完整性、電磁兼容性等多方面需求。
而以上種種,都在提示人們,智能化程度越高,對线束要求也將越嚴苛,隨之而來的將是成本、成本還是成本。
相較於智能駕駛對线束的顛覆,電力系統對线束的影響並未抵達盡頭。例如,去年开啓交付的Cybertruck上,特斯拉已自主研發85%控制器,並將在下一代平台中,完成對“老舊”控制器的全部升級,全部轉向48V電力系統。
從技術本身來看,電壓由12V升級到48V,高了四倍,理論上通過的電流就會更小,能夠減少傳遞過程中的損耗,並降低溫度,同時還能減少對线材直徑的需求。而更細的電线意味着更少的材料,就能降低线束的重量,從而降低成本。
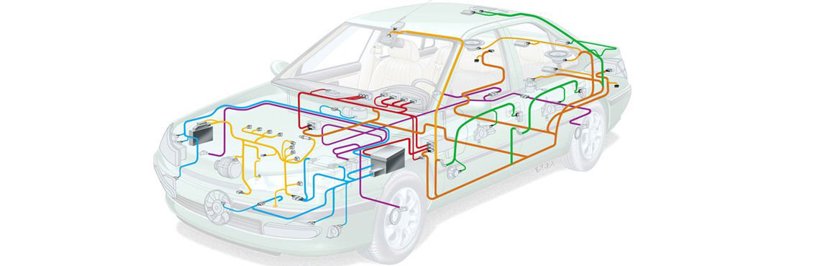
“盡管目前48V系統在整車上已有一些應用,但更多是在一些大功率回路上,如果將整車電網都切換爲48V,將對整車线束截面積有着巨大變化,這將可能推動整個汽車電氣系統的升級甚至是迭代。”吳劍如是說。
毫無疑問,汽車线束是最容易被忽略的安全部件。但隨着汽車電氣化、智能化的高速發展,线束變得至關重要。因此,他認爲,是時候打破陳規,讓线束供應商更早地參與到整車线束規劃設計中去。這樣才能更系統地提出輕量化、更完整且更精確的解決方案。
(本文來自於蓋世汽車Gasgoo)
標題:小米汽車偷工減料?看專家如何回應質疑
地址:https://www.utechfun.com/post/358803.html